Solving Common Challenges in Industrial Automation With Vending Hardware Solutions

You’re
likely no stranger to the challenges that come with industrial automation, from
managing inventory and reducing equipment downtime to automating maintenance
processes and streamlining supply chains. But what if there was a solution that
could help you tackle these issues head-on? Vending hardware solutions have
been gaining traction in recent years for their ability to effectively address
these common challenges. By integrating advanced technologies into your
operations, you can improve resource allocation, reduce costs, and increase
efficiency. But how exactly do these solutions work, and what benefits can you
expect to see in your own operations?
Streamlining Inventory Management
Streamlining inventory
management in industrial automation often starts with you identifying
inefficiencies in your current system. You can begin by analyzing your
inventory tracking process, looking for bottlenecks and areas where errors
often occur. Integrate vending hardware solutions that utilize vending
electrical systems and advanced vending sensor design to accurately track and
manage inventory levels. This can include automated dispensing systems that
monitor and control inventory usage in real-time. By implementing these
solutions, you can optimize inventory levels, reduce stockouts and
overstocking, and improve overall inventory accuracy. Effective inventory
management can have a significant impact on your operation’s productivity and
efficiency.
Reducing Equipment Downtime
In industrial automation,
optimizing inventory management is just one aspect of achieving operational
efficiency. You also need to minimize equipment downtime to maximize
production. Equipment failures can be costly and impact your bottom line. By
implementing a vending hardware solution, you can track and control the usage
of critical spares and supplies. This guarantees that you have the necessary
parts on hand to quickly repair or replace equipment, reducing downtime.
Additionally, you can set up alerts and notifications to inform maintenance
personnel of parts that need to be reordered or repaired, allowing you to stay
ahead of potential issues. This proactive approach helps you minimize equipment
downtime and maintain a competitive edge.
Automating Maintenance Processes
Your maintenance team’s
efficiency is crucial to minimizing equipment downtime and ensuring continuous
production. By automating maintenance processes, you can streamline task
management and reduce manual errors. Implementing a Computerized Maintenance
Management System (CMMS) helps you schedule and track maintenance activities,
ensuring that equipment is serviced before issues arise. Additionally,
integrating automated vending solutions for supplies and spare parts enables
your team to quickly access necessary materials. This reduces wait times and
allows them to focus on critical tasks. Real-time monitoring and alerts also
enable prompt intervention, minimizing equipment downtime and ensuring
production continuity. Automated maintenance processes help you optimize
resource allocation, improve response times, and enhance overall equipment
reliability.
Enhancing Supply Chain Efficiency
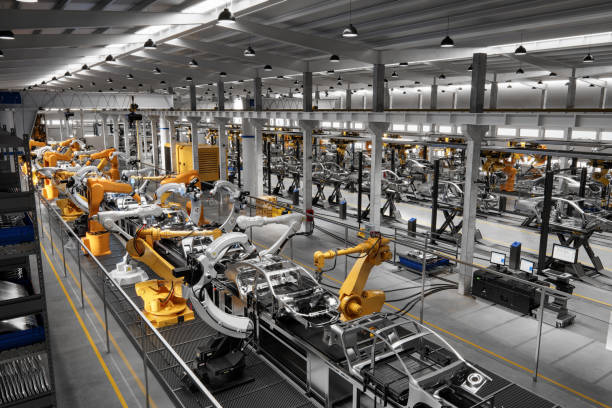
Industrial supply chains
are complex networks that require precise coordination and efficient logistics
to function smoothly. You can enhance supply chain efficiency by implementing
automated inventory management systems that utilize vending hardware solutions.
These systems enable real-time tracking of inventory levels, automated
ordering, and efficient distribution of supplies. By streamlining inventory
management, you can reduce stockouts, overstocking, and procurement lead times.
Additionally, vending hardware solutions can provide advanced analytics and
insights into inventory usage patterns, enabling you to optimize your supply
chain operations. By leveraging these solutions, you can improve supply chain
visibility, reduce costs, and increase overall efficiency. This, in turn, can
lead to improved profitability and competitiveness in your industry.
Optimizing Operational Productivity
Productivity is the
backbone of any successful industrial operation. You can substantially boost
productivity by optimizing operational workflows and streamlining tasks.
Implementing vending hardware solutions that track and manage inventory,
automate workflows, and provide real-time data analytics can help you achieve
this goal. These solutions enable you to monitor equipment usage, track
maintenance schedules, and identify areas for improvement. By leveraging
data-driven insights, you can optimize production processes, reduce downtime,
and enhance overall operational efficiency. Additionally, automating manual
tasks allows your workforce to focus on high-value tasks, further increasing
productivity. By optimizing operational productivity, you can gain a
competitive edge in the market and drive business growth.
Conclusion
By implementing vending hardware solutions,
you’ll effectively tackle common challenges in industrial automation. You’ll
streamline inventory management, reduce equipment downtime, and automate
maintenance processes. This integration also enhances supply chain efficiency
and optimizes operational productivity. As a result, you’ll experience improved
resource allocation, reduced costs, and increased overall efficiency. These
benefits will ultimately drive your business growth and competitiveness in
today’s fast-paced industrial landscape, giving you a distinct edge.
Comentarios
Publicar un comentario